Copper Ore Extraction and Mining
Firstly, the journey of copper refining begins with the extraction of copper from the rock or soil in its natural state, in an activity known as mining. Mining can be either open pit or underground. The open-pit method, also known as open-cast mining, involves removing the overlying earth and rocks to reach the underlying ore, usually perceived when deposits are located closer to the earth’s surface. On the other hand, underground mining, as the name suggests, involves extracting the ore from beneath the earth’s surface. This is usually the go-to method when the valuable deposits are located deep underground.
Once the copper ore is extracted, it typically contains a sizable amount of impurities. These impurities are naturally occurring waste rock or gangue minerals. Hence, a concentration process is required to remove these impurities and increase the concentration of copper in the ore.
Concentration Process
The primary method for the concentration process currently in use is froth flotation. In this process, copper ore is crushed and grinded to a fine powder and water is added to form a slurry. Next, detergents are added to the slurry causing the copper-bearing minerals to stick to air bubbles, which raise to the surface. Here, the copper concentrated froth is skimmed off the surface, leaving the rest of the waste material, referred as tailings, behind. This method allows for efficient recovery of copper minerals from relatively low-grade ore.
Smelting and Converting
After copper has been concentrated, it has to be smelted to transform it into a useful form that can be sold at the market. Copper concentrate is placed in a furnace where it is heated at high temperatures in the presence of oxygen. This leads to a series of chemical reactions that result in copper matte (consisting of copper, iron and sulfur).
The copper matte is then converted into blister copper during a process known as converting. In converting stage, it is heated intensely to remove majority of iron and sulfur. The result is an impure form of copper that has a blister-like surface, leading to its name blister copper.
Volatilizing and Electrolysis
The blister copper undergoes further refining in two stages: volatilizing and electrolysis. Volatilizing or fire refining involves passing the metal through a furnace to remove any remaining sulfur, oxygen or other impurities. The copper ends up with a purity of about 99%.
This copper undergo
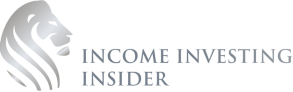